Understanding Porosity in Welding: Checking Out Causes, Effects, and Prevention Techniques
As specialists in the welding market are well mindful, understanding the reasons, impacts, and prevention methods associated to porosity is critical for achieving robust and trusted welds. By delving into the root causes of porosity, analyzing its damaging effects on weld top quality, and checking out effective avoidance techniques, welders can enhance their expertise and abilities to generate premium welds regularly.
Typical Reasons For Porosity
Contamination, in the form of dirt, oil, or rust on the welding surface area, develops gas pockets when heated up, leading to porosity in the weld. Inappropriate shielding occurs when the protecting gas, generally made use of in processes like MIG and TIG welding, is not able to completely protect the molten weld pool from reacting with the surrounding air, resulting in gas entrapment and succeeding porosity. Furthermore, inadequate gas coverage, frequently due to inaccurate circulation prices or nozzle positioning, can leave components of the weld unprotected, enabling porosity to create.
Effects on Weld Quality
The visibility of porosity in a weld can significantly endanger the total top quality and integrity of the bonded joint. Porosity within a weld produces spaces or dental caries that compromise the structure, making it a lot more vulnerable to cracking, corrosion, and mechanical failing.
Furthermore, porosity can prevent the efficiency of non-destructive screening (NDT) strategies, making it challenging to spot various other flaws or stoppages within the weld. This can cause significant security issues, particularly in crucial applications where the architectural integrity of the bonded parts is vital.

Avoidance Techniques Overview
Provided the damaging impact of porosity on weld top quality, efficient avoidance methods are crucial to maintaining the structural stability of bonded joints. Additionally, choosing the suitable welding criteria, such as voltage, existing, and travel speed, can aid minimize the threat of porosity development. By including these prevention techniques into welding methods, the event of porosity can be considerably lowered, leading to stronger and extra dependable welded joints.
Importance of Proper Protecting
Proper protecting in welding plays an important duty in stopping climatic contamination my link and making sure the honesty of bonded joints. Securing gases, such as argon, helium, or a mix of both, are commonly utilized to protect the weld pool from reacting with aspects airborne like oxygen and nitrogen. When these reactive aspects visit this page come right into contact with the hot weld swimming pool, they can create porosity, causing weak welds with reduced mechanical residential properties.
Insufficient protecting can result in various issues like porosity, spatter, and oxidation, compromising the structural stability of the bonded joint. Therefore, adhering to correct protecting try this practices is important to create premium welds with minimal issues and ensure the durability and dependability of the bonded parts (What is Porosity).
Surveillance and Control Methods
Just how can welders properly keep track of and regulate the welding process to ensure optimal results and prevent issues like porosity? By continually keeping an eye on these variables, welders can identify discrepancies from the suitable problems and make immediate adjustments to avoid porosity formation.

In addition, executing proper training programs for welders is necessary for keeping an eye on and managing the welding procedure properly. What is Porosity. Informing welders on the importance of maintaining consistent criteria, such as proper gas shielding and travel rate, can help avoid porosity concerns. Normal analyses and accreditations can also guarantee that welders excel in surveillance and regulating welding procedures
Moreover, making use of automated welding systems can enhance tracking and control capabilities. These systems can exactly control welding specifications, minimizing the chance of human error and making sure regular weld high quality. By incorporating innovative surveillance technologies, training programs, and automated systems, welders can properly monitor and manage the welding process to lessen porosity problems and attain premium welds.
Verdict
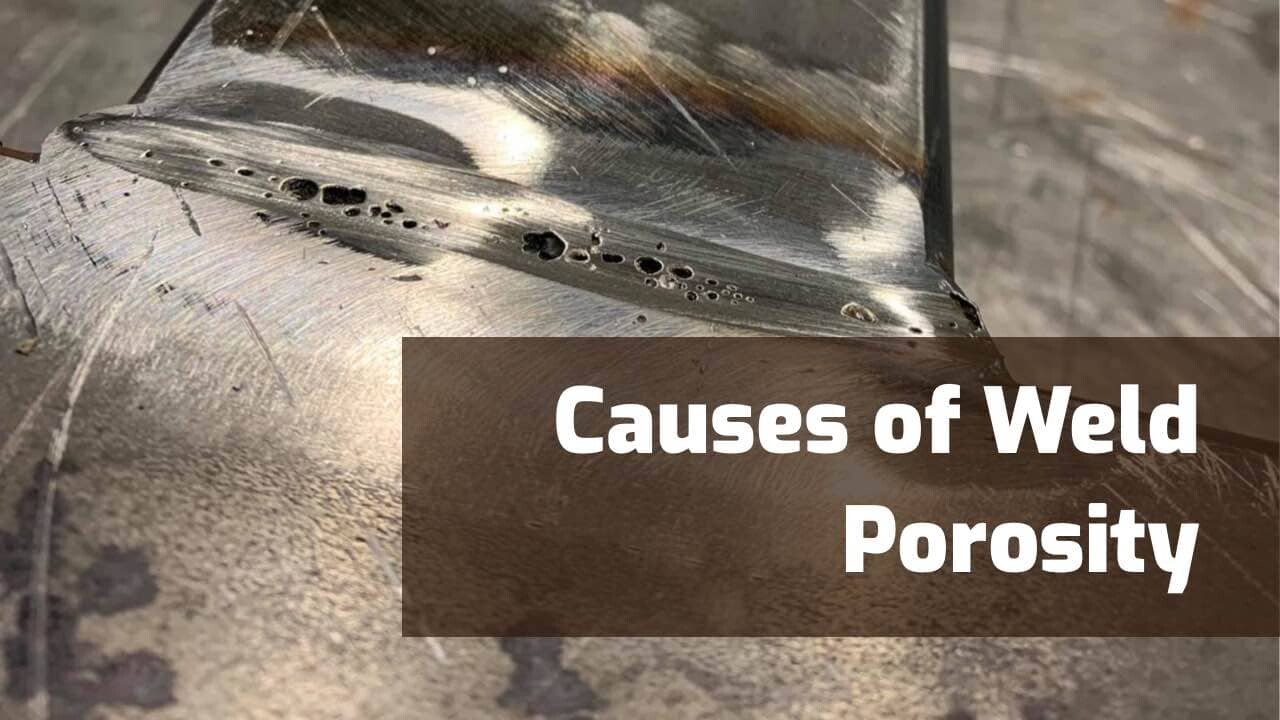
Comments on “Comprehensive Overview: What is Porosity in Welding and Just How to Prevent It”